2219 aluminum alloy is a heat-treatable strengthened aluminum alloy with high low temperature and room temperature strength, high temperature (below 300 â) lasting strength, excellent fracture toughness and stress corrosion resistance, etc. It is widely used in large aerospace structural parts . The connection method of aerospace structural parts is mainly welding. However, due to the characteristics of high thermal conductivity and low melting point of 2219 aluminum alloy, such as unreasonable parameter settings during welding, defects such as pores, cracks and deformation are easy to occur, especially in the fusion zone. It is easy to produce stomata impurities and so on. According to the reliability and cost control requirements of aerospace products, before welding large parts of 2219 aluminum alloy materials, it is necessary to use test pieces prepared from the same batch of materials to conduct welding tests to optimize the best welding parameters and avoid damage to large parts. During the welding process, the mechanical and welding properties of the material can also be evaluated and verified, which is the basis for the performance and quality level of the welded products for reference.
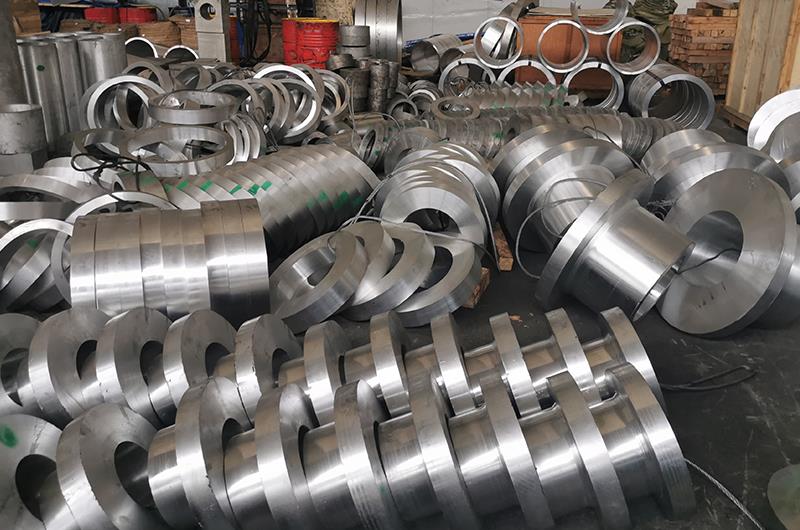
2219 aluminum alloy parts need helium arc priming before welding. Due to the helium arc bottoming welding, the molten pool is stable, and after cooling, a straight weld is formed, and the bottom is flat and bright. During the helium arc bottoming process of the 2219 aluminum alloy forging part (referred to as "2219 aluminum forgings"), the molten pool is boiling, and the bottom is matt color after cooling, and there is no flat bright band formed, which is a fault phenomenon.
Abnormal welding state The Bi content of 2219 aluminum alloy forging part exceeds the required value (<0.05%) of the GB/T3190-2008 standard, resulting in abnormal surface morphology of the weld after cooling. After quality review, there were operational errors in the production process, and the introduction of Bi-containing alloys in the batching process was the cause of the excessive Bi content in this forging.
In order to ensure that such failures do not occur again, the following rectification measures are proposed:
1) For welding raw materials, put forward the acceptance index requirements of low melting point metal elements such as Bi and Sn;
2) During the smelting process of raw materials, the main elements of the alloy smelted in the previous furnace should be used as the impurity elements in the furnace for the analysis and monitoring before the furnace for detection and analysis;
3) Strengthen the management and control of the storage, transportation and use of alloys and pure metals, and improve the detection range and detection capabilities of chemical components in the smelting process
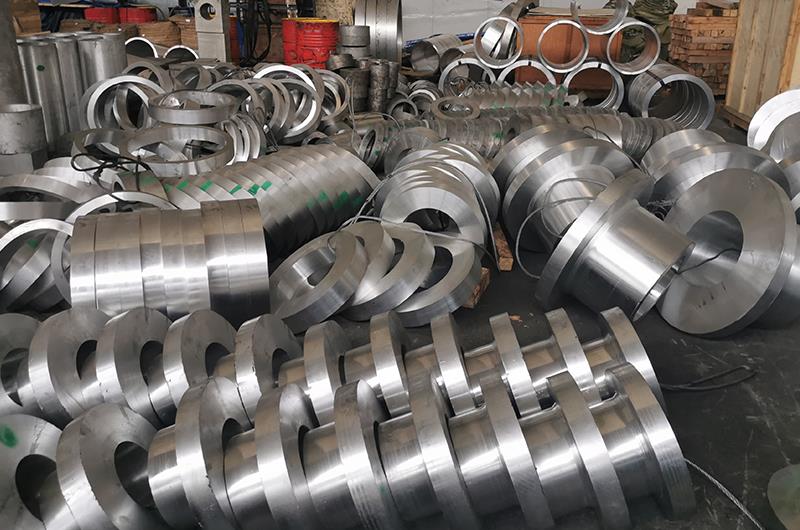
2219 aluminum alloy parts need helium arc priming before welding. Due to the helium arc bottoming welding, the molten pool is stable, and after cooling, a straight weld is formed, and the bottom is flat and bright. During the helium arc bottoming process of the 2219 aluminum alloy forging part (referred to as "2219 aluminum forgings"), the molten pool is boiling, and the bottom is matt color after cooling, and there is no flat bright band formed, which is a fault phenomenon.
Abnormal welding state The Bi content of 2219 aluminum alloy forging part exceeds the required value (<0.05%) of the GB/T3190-2008 standard, resulting in abnormal surface morphology of the weld after cooling. After quality review, there were operational errors in the production process, and the introduction of Bi-containing alloys in the batching process was the cause of the excessive Bi content in this forging.
In order to ensure that such failures do not occur again, the following rectification measures are proposed:
1) For welding raw materials, put forward the acceptance index requirements of low melting point metal elements such as Bi and Sn;
2) During the smelting process of raw materials, the main elements of the alloy smelted in the previous furnace should be used as the impurity elements in the furnace for the analysis and monitoring before the furnace for detection and analysis;
3) Strengthen the management and control of the storage, transportation and use of alloys and pure metals, and improve the detection range and detection capabilities of chemical components in the smelting process