7050 7150 Aluminum forgings forged product parts
7050 is a high strength Al-Zn-Mg-Cu alloy, which can be strengthened by heat treatment. On the basis of 7075 superhard aluminium alloy, the chemical composition of the alloy was adjusted, the content of zinc and copper was increased, the grain was refined by zirconium instead of chromium, and the content of impurities such as silicon and iron was reduced. Due to the optimization of chemical composition and the over-aging treatment, the aluminium alloy has high fatigue limit, good toughness, good stress corrosion resistance and good hardenability while maintaining high strength. Its hot working performance is similar to 7075 alloy. It has general weldability and good cutting property.
7050 is mainly used for high strength, good fracture toughness, and high stress corrosion cracking resistance and spalling corrosion of the main bearing structural parts, such as aircraft structure with thick plates, extrusions, free forgings and die forgings, such as aircraft structure with thick plates, extrusions, free forgings and die forgings, including fuselage frames, partitions, wing beams, landing gear support parts and rivets. Because the alloy has good hardenability, it is especially suitable for manufacturing large thick section parts. The supply state of the aluminum alloy includes T74, T76 and T73. T74 should be selected for structural parts requiring high strength and stress corrosion cracking resistance; T76 should be generally used for structural parts requiring high strength and anti-spalling corrosion; and T73 is mainly used for rivet materials requiring high strength and good corrosion resistance.
The Brinell hardness of 7050 aluminium alloy forging in T74 state is 158HBW.
7150 T77 aluminium forging forged product parts are an improved 7050 Alloy with high strength and good corrosion resistance. The fatigue resistance of 7150 T651 is 10%-15% higher than that of 7075, and the fracture toughness is 10% higher. The SCC resistance of 7150 T651 is similar to that of 7075. Mainly used in large passenger aircraft upper wing structure, body plate girder flange, upper outer panel main wing longitudinal beam, fuselage reinforcement, keel beam, seat guide rail.
Reduce heat treatment stress and avoid quenching deformation.
After solution treatment, the free forgings should be pre-compressed before artificial aging, and the permanent deformation is 1.5%-5.0%, so as to eliminate the internal stress.
The formability of the alloy is similar to that of 7075 aluminium alloy. If the initial forging temperature is too high, hot forging is easy to occur, which is disadvantageous to the hammer forging process.
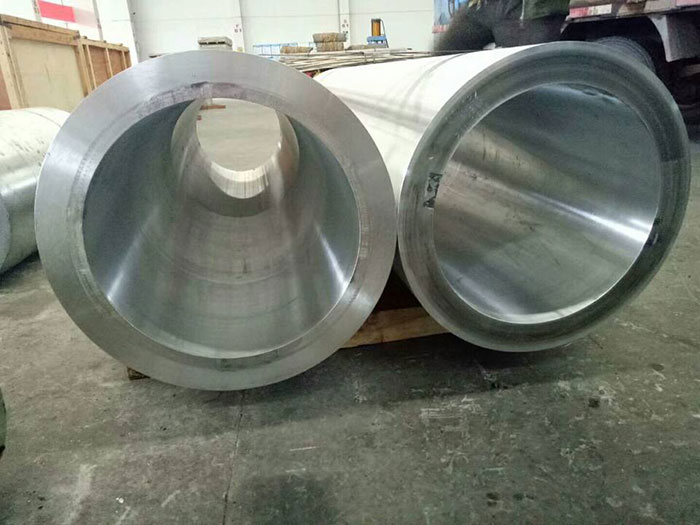
7050 is mainly used for high strength, good fracture toughness, and high stress corrosion cracking resistance and spalling corrosion of the main bearing structural parts, such as aircraft structure with thick plates, extrusions, free forgings and die forgings, such as aircraft structure with thick plates, extrusions, free forgings and die forgings, including fuselage frames, partitions, wing beams, landing gear support parts and rivets. Because the alloy has good hardenability, it is especially suitable for manufacturing large thick section parts. The supply state of the aluminum alloy includes T74, T76 and T73. T74 should be selected for structural parts requiring high strength and stress corrosion cracking resistance; T76 should be generally used for structural parts requiring high strength and anti-spalling corrosion; and T73 is mainly used for rivet materials requiring high strength and good corrosion resistance.
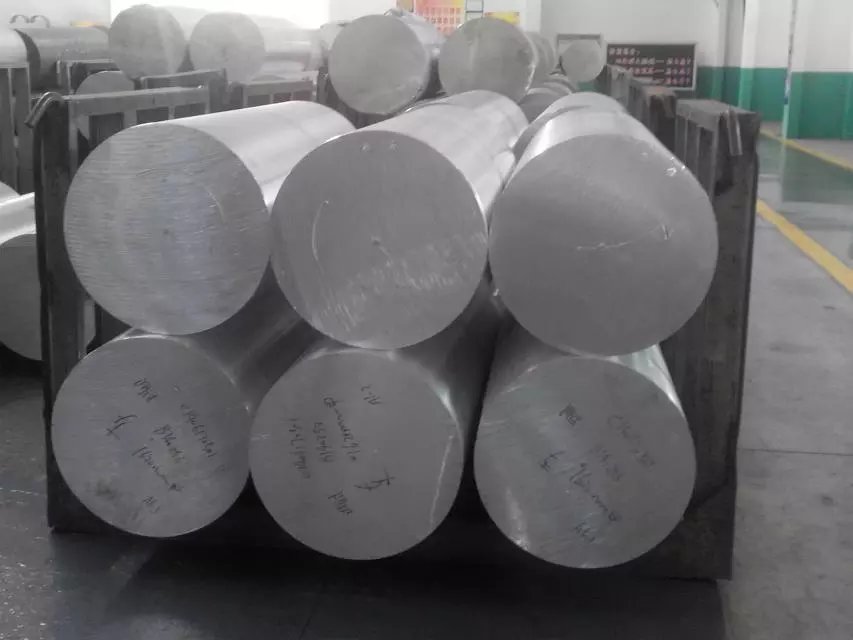
The Brinell hardness of 7050 aluminium alloy forging in T74 state is 158HBW.
7150 T77 aluminium forging forged product parts are an improved 7050 Alloy with high strength and good corrosion resistance. The fatigue resistance of 7150 T651 is 10%-15% higher than that of 7075, and the fracture toughness is 10% higher. The SCC resistance of 7150 T651 is similar to that of 7075. Mainly used in large passenger aircraft upper wing structure, body plate girder flange, upper outer panel main wing longitudinal beam, fuselage reinforcement, keel beam, seat guide rail.
Reduce heat treatment stress and avoid quenching deformation.
After solution treatment, the free forgings should be pre-compressed before artificial aging, and the permanent deformation is 1.5%-5.0%, so as to eliminate the internal stress.
The formability of the alloy is similar to that of 7075 aluminium alloy. If the initial forging temperature is too high, hot forging is easy to occur, which is disadvantageous to the hammer forging process.
Tensile Properties of 7050 Aluminum Alloy T73652 Free Forging at Room Temperature |
|||||
Thickness/mm | Direction | Tension strength Rm/MPa | Prescribed plastic elongation strength Rp0.2/MPa |
Provision of non-proportional compressive strength Rpc0.2/MPa |
Elongation A (%) |
≤50 | Portrait | 496 | 434 | 441 | 9 |
Long transverse | 490 | 421 | 448 | 5 | |
>50--75 | Portrait | 496 | 427 | 434 | 9 |
Long transverse | 483 | 414 | 441 | 5 | |
Short transverse | 462 | 379 | 421 | 4 | |
>50--110 | Portrait | 483 | 421 | 427 | 9 |
Long transverse | 476 | 407 | 434 | 5 | |
Short transverse | 455 | 379 | 421 | 4 |
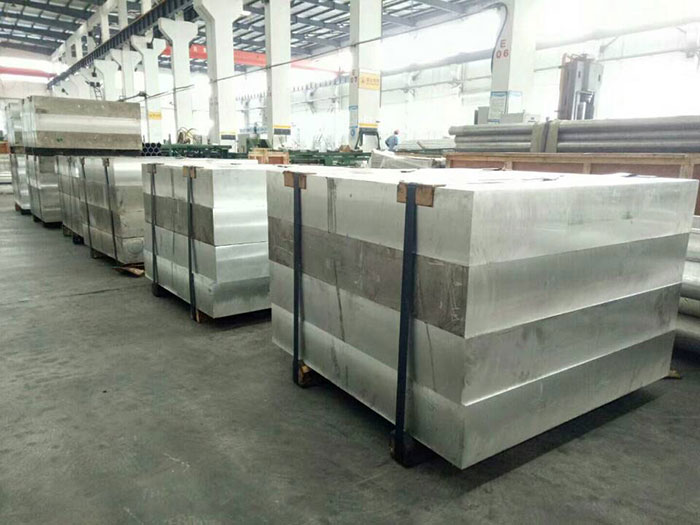
7050 7150 Chemical Composition | |||||||||||||
Alloy | Si | Fe | Cu | Mn | Mg | Cr | Ni | Zn | Ti | Zr | Others | Al | |
Single | Total | ||||||||||||
7050 | 0.12 | 0.15 | 2.0~2.6 | 0.10 | 1.9~2.6 | 0.04 | ~ | 5.7~6.7 | 0.06 | 0.08~0.15 | 0.05 | 0.15 | Rest |
7150 | 0.12 | 0.15 | 1.9~2.5 | 0.10 | 2.0~2.7 | 0.04 | ~ | 5.9~6.9 | 0.06 | 0.08~0.15 | 0.05 | 0.15 | Rest |
Room Temperature Tensile Properties of Aluminum Alloy T736 State Die Forging | |||||
Thickness/mm | Direction | Tension strength Rm/MPa | Prescribed plastic elongation strength Rp0.2/MPa |
Provision of non-proportional compressive strength Rpc0.2/MPa |
Elongation A (%) |
≤50 | portrait | 496 | 427 | 434 | 7 |
transverse | 469 | 386 | 400 | 5 | |
>50--100 | portrait | 490 | 421 | 434 | 7 |
transverse | 462 | 379 | 393 | 4 | |
>100--125 | portrait | 483 | 414 | 434 | 7 |
transverse | 455 | 372 | 379 | 3 |
Tensile Properties of 7050 Aluminum Alloy T736 State Die Forging at Room Temperature | |||||
Thickness/mm | Direction | Tension strength Rm/MPa | Prescribed plastic elongation strength Rp0.2/MPa |
Provision of non-proportional compressive strength Rpc0.2/MPa |
Elongation A (%) |
≤50 | portrait | 496 | 427 | 434 | 7 |
transverse | 469 | 386 | 400 | 5 | |
>50--100 | portrait | 490 | 421 | 434 | 7 |
transverse | 462 | 379 | 393 | 4 | |
>100--125 | portrait | 483 | 414 | 434 | 7 |
transverse | 455 | 372 | 379 | 3 |
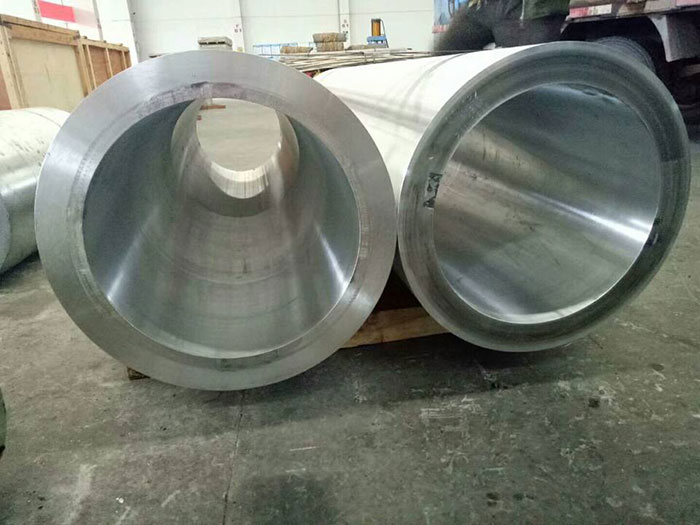
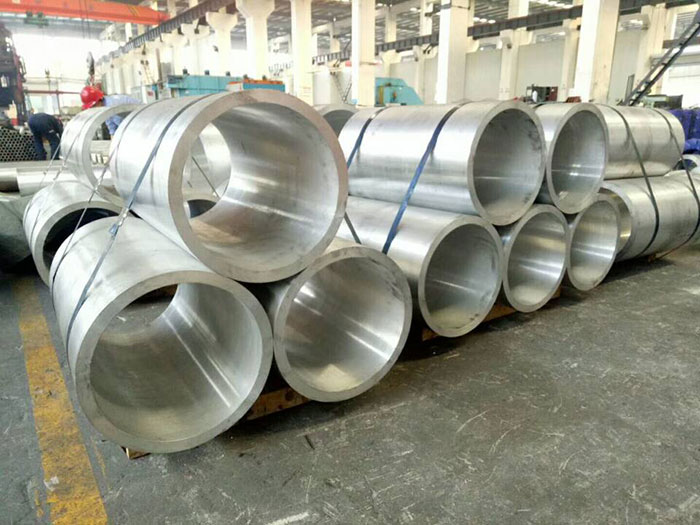
Low Temperature Tensile Properties of 7050 Aluminum Alloy Forgings | ||||
Alloy Temper | Temperature | Tension Strength Rm/MPa | Prescribed plastic elongation strength Rp0.2/MPa |
Elongation A (%) |
7050 T73652 | -195 | 662 | 572 | 13 |
-80 | 586 | 503 | 14 | |
-28 | 552 | 476 | 15 |
Tensile Properties of 7050 Aluminum Alloy Forgings at High Temperature | |||||
Alloy Temper | Temperature/â | holding time/h | Tension Strength Rm/MPa | Prescribed plastic elongation strength Rp0.2/MPa |
Elongation A (%) |
7050 T73652 | 24 | - | 524 | 455 | 15 |
100 | 0.1--10 | 462 | 427 | 16 | |
100 | 469 | 434 | 16 | ||
1000 | 462 | 427 | 17 | ||
150 | 0.1 | 414 | 386 | 17 | |
10 | 407 | 386 | 18 | ||
100 | 365 | 352 | 20 | ||
1000 | 290 | 276 | 23 | ||
175 | 0.1 | 379 | 345 | 19 | |
10 | 324 | 310 | 22 | ||
100 | 248 | 234 | 25 | ||
1000 | 193 | 172 | 31 | ||
205 | 0.1 | 324 | 290 | 22 | |
10 | 221 | 207 | 27 | ||
100 | 165 | 152 | 32 | ||
1000 | 131 | 110 | 45 |